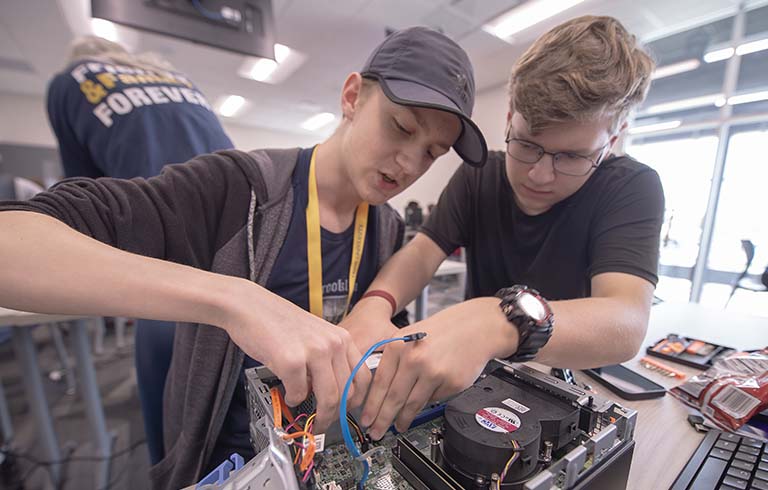
Trine engineering, computing camps draw more than 50 students
Trine University hosted more than 50 high school students at its 2025 Allen School of Engineering and Computing summer camps.
May 06, 2025
This year’s challenge for the national competition was to produce a replica of one of George Washington’s swords, or design one based on his known preferences and needs.
The Trine team, dubbed “Foundry of Freedom,” decided to create a copy of Washington’s cuttoe sword. Washington acquired the sword, which sports a lion’s head, in 1770, just prior to the Revolutionary War.
The team earned second place in the “Best Authentic George Washington's Sword” category and third place for “Best Casting” and “Best Design and Process.”
The competition was held April 12 in Atlanta. Sponsored by the Steel Founders’ Society of America and now in its seventh year, Cast in Steel is inspired by the History Channel series “Forged in Fire.”
That show challenges smiths to forge bladed weapons.
The Trine team was made up of mechanical engineering majors Nikolas Uhler of Charlottesville, Indiana, Rhett Laud of Lake Village, Indiana, Reese Greene of Leo, Indiana, and Nathaniel DiRe of Southport, North Carolina.
Sparks fly
Uhler said he was drawn to the project by the opportunity to pour hot metal.
“Seeing the sparks fly everywhere looked like fun,” he said.
Greene said the team focused on historical accuracy, realistic design for casting characteristics and staying within the requirements of the competition.
“We had no idea what tests they might do before the actual day of the competition, so we had to choose something that we thought could do everything,” he said. “There were three designs we could realistically choose from: broad sword, small sword, or cuttoe.”
“We thought the broad sword could do everything but would be too heavy. The small sword would be both too difficult to cast and far too weak with its thin geometry. However, the cuttoe seemed to be the most balanced choice, and historically it was chosen as a very functional weapon.”
Once the selection was made, the team used CAD software to model the blade and performed structural analysis to simulate loading conditions and ensure the blade could withstand expected stresses.
“Based on our simulations, we designed and refined a gating system to ensure complete metal flow during casting and to prevent premature solidification,” said Uhler.
The handle was modeled using a combination of CAD and Blender, with the goal to create a near-exact replica of George Washington’s lion-headed cuttoe for historical accuracy and visual appeal.
The team 3D-printed a blade that was used to create a match plate and flask for sand casting.
Investment casting
They chose investment casting to make the other pieces, since that process provides very accurate tolerances and clean surface finishes.
“This makes it ideal for parts that are meant to be beautiful,” said Greene.
The team assembled 3D-printed patterns on a tree, applied multiple ceramic slurry coats and then burned out the patterns before pouring molten metal.
No one had tried investment casting at Trine for nearly a decade. Greene said the extra time involved in the process created some challenges.
“Coating is what takes the most time,” he said. “If you don’t let it dry enough between layers, moisture can be trapped and cause layers to be weaker and crack when heating for melt and burn out.”
At one point, he said, he tried to rush the process and five of six pommels he was producing failed.
“Fortunately, everything came out well and the single pommel was successful,” he said.
Uhler said the group also had trouble filling the first couple of iterations of the blade and had to modify its gating multiple to get everything to work.
All the components underwent secondary machining and finishing to meet final geometry specifications, then were assembled using high-strength epoxy.
Early exit
Unfortunately, the sword’s blade broke in the first round, along with about one-third of its competitors.
The team received an unofficial shout-out during the awards from judge Ben Abbott, who also serves as a judge on “Forged in Fire” for “Best Performance award: The sword that broke my heart.”
“To me, this was almost as good as getting in the top three during the filmed portion of the competition,” said Greene. “Personally, achieving second in historical accuracy was exhilarating. That was everything I worked for and desired during the design and development of this blade, and I am incredibly grateful to receive it.”
“Since our sword broke in the first round, we are a bit disappointed in our performance, but our sword looked really good and we wrote a good paper, so we are proud of that,” agreed Uhler.