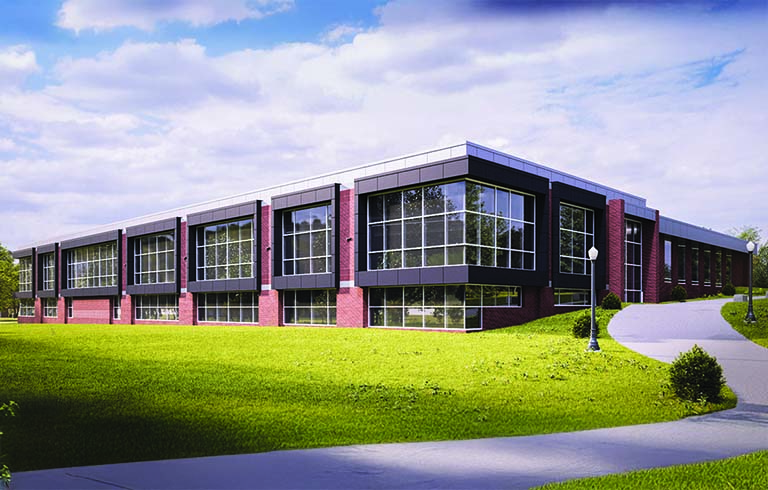
Trine University receives contribution from Honda toward Pellegrino Center
Trine University has received a $100,000 contribution from Honda toward its new John and Mary Pellegrino Student Design and Training Center (Pellegrino Center).
May 14, 2025
The project gave students the opportunity to apply their design, fabrication and project management skills to a real-world engineering challenge, bringing a multi-year collaboration to a successful finish.
“The sole purpose of the pallet squeezer is to realign a stack of pallets that get disturbed during transportation. This required applying knowledge in machine component design, hydraulic systems and finite element analysis, among many other skills. I haven’t seen this much fabrication work on campus with any other project,” explained Gurudutt Chandrashekar, Ph.D., assistant professor and senior design advisor.
The 2023-24 design team completed the engineering and partial fabrication of the system, but delays in material delivery—particularly heavy steel sheets and structural tubing—meant the build was only about one-third complete by the end of their final semester. The 2024-25 senior team stepped in to finish the job, working closely with Dexter Group to understand the project's goals and requirements.
Hands-on experience
The team included Gabriel Luke of Houston, Texas, Blake Lude of Auburn, Indiana, Tucker Hasselman of Pleasant Lake, Indiana, Caleb Brown of Coldwater, Michigan, and Dillon Sims of Curtice, Ohio.
Their work focused on completing the remaining fabrication and preparing the pallet squeezer for on-site testing.
For many of the students, the opportunity to get hands-on experience was what initially drew them to the project.
“I enjoyed the build phase of this project very much,” said Hasselman. “I did a large part of the welding, cutting and fabricating of parts for the squeezer, which is the kind of hands-on work that I like.”
“I was responsible for using the waterjet cutter to fabricate several steel components,” added Brown. “Learning how to use the waterjet and designing parts for it was a valuable experience.”
Lude appreciated the challenge of joining a project already in progress.
“Because this was a multi-year project, our group had to pick up someone else’s design,” he said. “I enjoyed figuring out how to carry that design forward and create solutions when we ran into barriers.”
Applying a Trine education to a real problem
Throughout the build phase, students applied technical and teamwork skills developed from previous coursework.
“Reviewing the previous group’s designs and performance simulations helped ensure all parts were fabricated correctly, within tolerances, and could withstand operating conditions,” Brown noted. “This project was a great way to apply those concepts.”
“Senior design is a great simulation for a full-time engineering job,” added Lude. “It requires you to work with a customer and go through the full engineering design process. The communication, teamwork and hands-on skills were all essential.”
Once fabrication was complete, the team conducted functionality testing at Trine using brick-loaded sample pallets to simulate field conditions.
Additional testing, including strength and load capacity assessments, was completed on-site at Dexter. The company reported back that the unit is performing as intended.
Dexter is expected to see direct operational benefits from the student-built machine, which reduces the time required to unload brake drums and helps streamline its manufacturing process. The company plans to design and construct multiple pallet squeezers based on the team’s design.
Skills that translate to careers
The team members see their experience on the project as a strong foundation for their future careers.
Both Lude and Sims are looking for manufacturing positions in the Midwest, where Lude feels he’ll be able to use what he’s learned to help troubleshoot equipment.
“Being able to build something yourself is great practice for spotting and preventing design flaws early,” he stated.
“Project management skills from this project will help me greatly,” said Hasselman, who has accepted an offer with Shambaugh and Sons as a fire protection engineer.
Brown starts work this month as a project engineer at MAGMA Foundry Technologies.
“Communication in a team environment will be critical in my role,” he added.
Luke’s plan takes an alternate route that starts with joining the Marines and later pursuing a career in the automotive industry.
“The fabrication experience will come in handy wherever I end up,” he mentioned.
As Dr. Chandrashekar noted, “These students took on a complex, multi-year challenge and delivered a professional-grade solution. Their dedication and teamwork exemplify the hands-on, industry-relevant experience we strive to provide at Trine.”